Predictive maintenance has become an important way for big industries to make sure their operations run smoothly and continuously. This cutting-edge method uses data analytics and artificial intelligence to predict when equipment might break down before it does.
Moving from being reactive to being proactive lets businesses plan repairs for times when they’re not busy, which saves money and makes machines last longer.
But what tools are behind this practice and how do large-scale industries use them to get the best results? Let’s look into it more.
Why Predictive Maintenance is Important
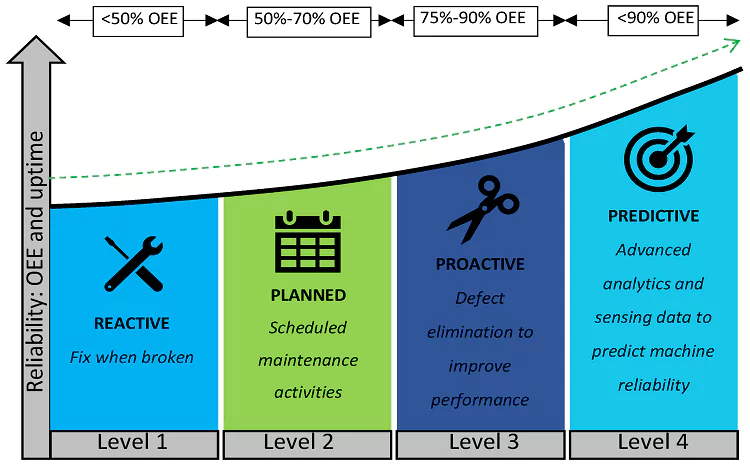
Predictive maintenance is an important part of modern businesses because it keeps them from getting to deal with expensive downtime and increases their overall efficiency.
For example, food or drug companies can plan repair for off-peak hours by guessing when machinery like stainless steel buttertanks might break down. This keeps operations running smoothly.
Predictive maintenance stops problems before they happen. This lowers the chance that equipment will break down without warning, which can cause big delays in production, cost overruns, and even safety risks.
Moreover, predictive maintenance can save a lot of money in the long run by making machines and systems last longer.
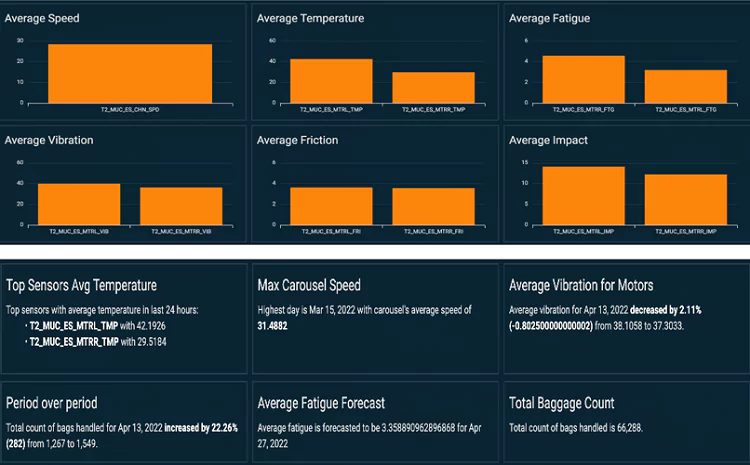
What Makes Up Predictive Maintenance
Data collection, analysis, and implementation methods are often important parts.
Collecting data means getting details from many places, like sensors on machinery, logs, or notes from operators. It’s very important because it’s what predictions are based on.
Next comes the analysis. This is where complex programs look through the data and find patterns and trends. They use this data to guess what failures will happen in the future, which lets companies plan ahead.
Technologies That Make Predictive Maintenance Possible
The success of predictive maintenance depends on using cutting-edge technologies that let you keep an eye on machines and find problems before they happen.
For example, Internet of Things (IoT) devices are often used to collect data from machines in real time. This data can then be studied to figure out when machines will break down.
Another important tool is machine learning algorithms, which can learn from past data to find trends and guess what problems might happen in the future.
Digital twin technology also lets physical assets be virtually copied, which lets operators find possible problems without stopping operations.
Big data analytics help businesses make sense of huge amounts of data by pulling out insights that can be used to avoid unplanned downtime.
Together, these technologies make predictive maintenance possible, which keeps the business running.
Implementing Predictive Maintenance in Big-Scale Industries
The first step in this process is adding new tools to the ones they already have. To do this, maintenance tactics need to change from being reactive to being proactive.
The first step is to put sensors and other devices on the equipment, so it can collect and keep an eye on real-time data. Then, tools for data analysis are added to make sense of this information, find trends, and guess what might go wrong.
This is often done with artificial intelligence and machine learning systems.
Making a proactive action plan is the last step. This plan is meant to deal with possible problems before they get worse, so everything runs smoothly.
Staff training is also very important for this process because teams need to know how to use these new tools correctly.